Denwor54
Life of the Party
I used to jigs when I was in the woodworking trade and thought I would show some of the jigs that I use. When I first started this journey I quickly started playing around with different jigs to help make the assembly easier. I became frustrated with hand reaming the cork pieces and had realized I had to make jig for the cork inlay for the reel seat. Now I use the jig for reaming the cork pieces which has worked out well. I’m curious what jigs you guys have assembled for your bamboo rod building needs.
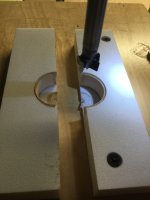
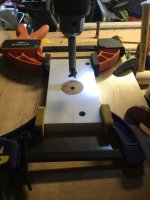
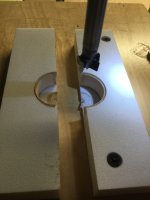
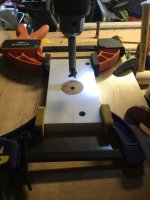